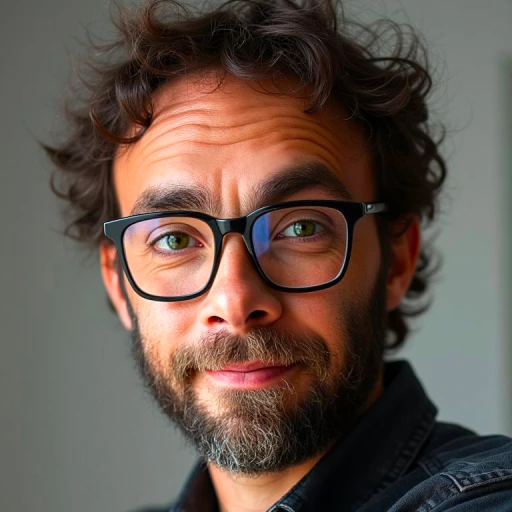
Comprendre l'AMDE
L'analyse des modes de défaillance et de leurs effets, communément appelée AMDE ou FMEA, est une méthode cruciale utilisée dans l'industrie pour identifier et évaluer les risques potentiels liés aux défaillances d'un système ou d'un produit. Cet outil de gestion de la qualité facilite la compréhension des modes de défaillance et de leurs conséquences possibles sur le produit et le processus. En intégrant l'analyse FMEA, les entreprises peuvent anticiper les problèmes de qualité et ainsi améliorer leur évaluation approfondie des risques.
Les principes fondamentaux de l'AMDE
La méthode FMEA repose sur plusieurs étapes clés pour son implémentation :
- Identification des modes de défaillances : Déterminer les différentes causes possibles de défaillance dans un produit ou un process.
- Évaluation de la gravité des effets : Analyser les conséquences de chaque mode de défaillance sur le produit et le système global.
- Analyse des causes potentielles : Examiner les causes qui pourraient entraîner ces défaillances.
- Évaluation des actions correctives : Développer des mesures pour atténuer ces risques.
Cette analyse approfondie des risques permet d'éviter les défaillances potentielles par la mise en œuvre d'actions préventives.
Les avantages de l'AMDE pour l'industrie
Les atouts déterminants de l'AMDE dans l'industrie
Dans un environnement industriel en perpétuelle évolution, l'analyse des modes de défaillance et de leurs effets (AMDE) joue un rôle crucial pour les entreprises soucieuses de la qualité optimale de leurs produits et processus. En facilitant l'identification anticipée des défaillances potentielles, cette méthode permet non seulement de minimiser les risques, mais également de renforcer l'efficacité globale des systèmes de gestion de la qualité.
L'un des principaux avantages de l'AMDE est sa capacité à fournir une vue d'ensemble claire des modes de défaillance potentiels dans un système ou un produit. Cela se fait par une analyse méticuleuse des divers processus, incluant chaque étape critique où une défaillance pourrait survenir. En identifiant les modes de défaillances, les entreprises sont mieux équipées pour mettre en place des actions correctives adaptées et ainsi, prévenir des effets indésirables avant qu'ils ne se manifestent.
De surcroît, l'application efficace de l'AMDE stimule la prise de décisions éclairées dans le domaine de la gestion de la qualité. Les analyses détaillées permettent de cerner précisément les causes des défaillances, offrant ainsi aux responsables qualité l'opportunité de prioriser les actions en fonction de la gravité et de la probabilité des risques identifiés. Ce processus, couramment appelé amdec fmea, s'intègre parfaitement dans les stratégies de gestion proactive des risques, contribuant ainsi à l'amélioration continue de la qualité et à la satisfaction du client final.
Enfin, l'efficacité de l'AMDE repose également sur la méthode de formation des équipes concernées. Il est essentiel d'assurer une compréhension commune des concepts clés tels que l'amdec produit, l'amdec inversee et le fmea amdec à travers des formations ciblées et des outils pédagogiques adaptés. Cela permet aux entreprises d'assurer une mise en œuvre réussie de l'AMDE, garantissant ainsi une amélioration continue des produits et processus.
Implémentation efficace de l'AMDE
Étapes clés pour un déploiement réussi de l'AMDE
Le succès de l'implémentation de l'analyse des modes de défaillance et de leurs effets (AMDE) repose sur une approche méthodique et structurée. Comprendre les bases de l'AMDE et ses avantages nous amènent naturellement à envisager comment la mettre efficacement en œuvre dans l'industrie. Voici les étapes essentielles qui garantissent son efficacité :1. Compréhension des risques et des modes de défaillances
Il est crucial d'identifier d'abord les modes de défaillances potentiels et de comprendre leurs effets sur le produit ou le processus. Cette étape nécessite une bonne formation et une analyse approfondie pour évaluer la gravité et l'impact des défaillances. Une évaluation approfondie des risques pour garantir la qualité dans l'industrie est essentielle pour assurer une détection optimale.2. Constitution de l'équipe interdisciplinaire
Une équipe bien formée, incluant divers experts des secteurs clés de l'entreprise, est indispensable pour un AMDEC processus réussi. Les membres doivent travailler ensemble pour identifier les causes et analyser les risques associés aux défaillances potentielles. Cette collaboration garantit une analyse fmea exhaustive.3. Identification et hiérarchisation des défaillances
Utilisez la méthode FMEA pour identifier les modes de défaillance possibles. Il est important de hiérarchiser ces modes selon leur gravité, leur occurrence et leur détection. Cela permet de concentrer les efforts sur les risques les plus critiques.4. Développement et mise en place d'actions correctives
Une fois les défaillances identifiées, il est temps de mettre en œuvre des actions correctives. Ces actions doivent être précises et bien planifiées pour éviter la récurrence des problèmes et améliorer la qualité du produit ou du processus.5. Suivi et réévaluation continue
Après la mise en œuvre initiale, il est essentiel de suivre l'efficacité des actions prises et d'ajuster en conséquence. Une amdec produit ou processus peut bénéficier d'une réévaluation régulière pour s'adapter aux évolutions du système ou des produits. L'implémentation de l'AMDE est un processus continu nécessitant un engagement constant de la part de l'entreprise. Un contrôle rigoureux et des ajustements constants permettent d'optimiser la qualité et de minimiser les défaillances potentielles. Pour en savoir plus sur l'importance de ce rôle au sein de l'industrie, consultez l'importance du rôle du contrôleur qualité.Études de cas réussies
Exemples d'AMDE réussies dans l'industrie
La mise en application de l'AMDE (Analyse des Modes de Défaillance et de leurs Effets) dans divers secteurs industriels a montré des résultats probants, offrant des leçons essentielles sur la manière d'améliorer la qualité et la fiabilité des produits et processus. Voici quelques exemples inspirants :- Industrie automobile : Un fabricant de véhicules a appliqué la méthode AMDEC (Analyse des Modes de Défaillance, de leurs Effets et de leur Criticité) pour analyser le processus de fabrication des transmissions. En identifiant les modes de défaillance potentiels et leurs causes profondes, l'entreprise a pu réduire le nombre de défaillances et augmenter la satisfaction client.
- Électronique : Une entreprise spécialisée dans les semiconducteurs a introduit l'AMDEC produit pour détecter les effets des défaillances dans ses composants sévèrement intégrés. Grâce à cette analyse rigoureuse, des actions correctives ont été mises en place, abaissant le taux de défauts et améliorant la qualité générale des produits finis.
- Pharmaceutique : La mise en œuvre de l'AMDEC process a permis à une société pharmaceutique d'identifier les risques associés à un nouveau procédé de fabrication. En évaluant la gravité et la fréquence des modes défaillants, le système a permis de renforcer la sécurité des produits tout en minimisant les défaillances potentiels pendant la production.
- Aéronautique : Dans l'aviation, l'application de l'AMDEC fmea a permis à une entreprise de contrôler rigoureusement ses processus de maintenance des avions. En analysant les modes de défaillances critiques, ils ont optimisé les intervalles de maintenance et étendu la durée de vie de leurs équipements, confirmant l'efficacité de l'AMDE dans la gestion du risque.
Défis courants et solutions
Défis rencontrés lors de la mise en œuvre de l'AMDE dans l'industrie
L'analyse des modes de défaillance et de leurs effets (AMDE) est un outil puissant pour améliorer la qualité des produits et processus. Cependant, sa mise en œuvre n'est pas exempte de défis. Voici quelques obstacles courants et des solutions pour les surmonter :- Complexité du processus : L'un des obstacles majeurs est la complexité inhérente à l'AMDE. La méthode AMDEC demande une compréhension approfondie des processus et des systèmes pour identifier efficacement les défaillances potentielles et leurs effets. La formation du personnel sur la méthode FMEA et l'implication des experts à chaque étape du processus sont cruciales pour minimiser ce défi.
- Identification des modes de défaillance : Un autre défi consiste à identifier de manière exhaustive les modes défaillances possibles. Cela peut être surmonté en réunissant une équipe multidisciplinaire pour une analyse approfondie des causes et en utilisant une approche collaborative pour évaluer les modes défaillance potentiels et mettre en place des actions correctives.
- Évaluation de la criticité : La détermination de la gravité des défaillances et de leurs effets sur le produit processus est essentielle pour prioriser les actions. Un système structuré d'évaluation de la criticité aide à garantir l'efficacité de l'AMDEC produit. Adopter une approche de priorisation claire basée sur les critères de gravité, d'occurrence et de détection peut améliorer ce processus.
- Intégration dans les systèmes existants : Intégrer l'AMDEC FMEA dans les systèmes de qualité existants peut être complexe. La mise en œuvre progressive, en s'assurant que le processus d'entreprise est aligné avec les objectifs de l'analyse risques, permettra une transition plus fluide. La communication continue et l'alignement des objectifs d'entreprise sont également essentiels pour réussir l'intégration.
- Suivi et mise à jour : Enfin, garantir que l'AMDEC processus reste un document vivant nécessite une attention régulière. Cela implique de réviser régulièrement les analyses pour intégrer de nouvelles données et mettre en œuvre des amdec inversées si nécessaire pour répondre aux exigences changeantes du marché et des produits.
L'avenir de l'AMDE dans l'industrie
Évolution des outils et intégration numérique
Dans un environnement industriel en constante évolution, l'analyse des modes de défaillance et de leurs effets (AMDE) doit également s'adapter pour rester pertinente. L'introduction de la transformation numérique offre des opportunités considérables pour améliorer l'AMDE. Par exemple, l'intégration d'outils numériques avancés dans le processus permet d'accroître la précision de la détection des modes de défaillance potentiels grâce à l'automatisation et à l'analyse de données en temps réel.
Rôle de la formation continue
La formation est cruciale pour tirer pleinement parti des méthodes telles que l'AMDEC et l'AMDEC inversée. Les entreprises doivent investir dans l'amélioration des compétences de leur personnel afin qu'ils maîtrisent les méthodes FMEA et peuvent s'adapter aux nouvelles technologies et méthodes d'analyse des risques. Une bonne formation permet également de mieux comprendre et gérer la gravité des défaillances potentielles, en identifiant efficacement les causes et en planifiant des actions correctives appropriées.
Amélioration continue du système qualité
L'AMDE doit être envisagée comme une étape d'un processus d'amélioration continue. Les leçons apprises des analyses précédentes doivent être intégrées dans le cycle du produit processus pour renforcer la robustesse et l'efficacité du système de qualité. En conservant une documentation rigoureuse des modes de défaillances et des actions mises en place, les entreprises assurent la pérennité de leurs systèmes face aux risques potentiels.
Collaboration accrue entre équipes
Pour que l'implémentation de l'AMDE soit un succès, l'interaction et la communication entre les différentes équipes au sein de l'organisation sont essentielles. Cela concerne particulièrement les ingénieurs, les responsables qualité et les gestionnaires de production qui doivent travailler ensemble pour intégrer efficacement l'analyse modes défaillances à chaque étape du processus. Une collaboration efficace garantit que les défaillances sont identifiées et traitées rapidement, minimisant ainsi les impacts sur le produit et la productivité de l'entreprise.