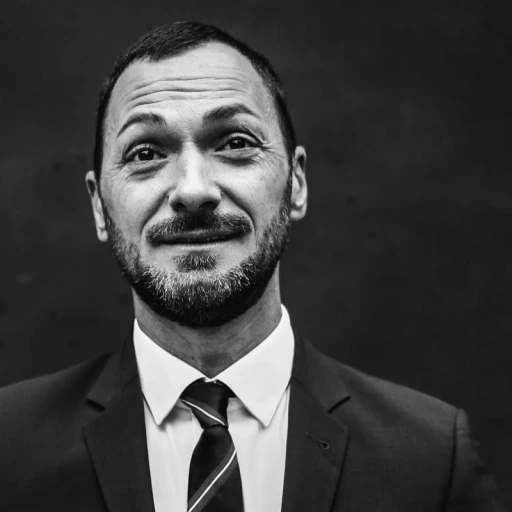
Comprendre le processus PPAP
Qu'est-ce que le processus PPAP et pourquoi est-il essentiel ?
Le processus PPAP, ou Production Part Approval Process, est une méthode cruciale dans l'industrie pour garantir la qualité des produits avant qu'ils ne soient approuvés pour la production en série. Cette démarche, bien qu'elle puisse sembler complexe, joue un rôle déterminant pour assurer que les pièces produites respectent les spécifications et les attentes du client, tout en prévenant les problèmes potentiels en amont du processus de fabrication.
Principalement développée dans l'industrie automobile, le PPAP requiert une optimisation des processus constante pour s'adapter aux besoins croissants de qualité et de conformité. Il s'agit d'un outil de communication entre fournisseurs et clients, assurant que tous les acteurs impliqués ont une compréhension claire des exigences concernant le produit et le processus de production.
En intégrant la méthodologie APQP (Advanced Product Quality Planning) dans le processus PPAP, les entreprises peuvent établir un plan de contrôle détaillé, incluant l'analyse des modes de défaillance et leurs effets, ce qui est indispensable pour atteindre un niveau de qualité constant. Grâce à des documents justificatifs tels que le dossier PPAP et la soumission PPAP, le fournisseur prouve au client que la conception et le processus de fabrication sont capables de produire le produit selon les exigences spécifiées.
Le processus PPAP permet également d'assurer une production continue sans interrompre la chaîne d'approvisionnement, tout en veillant à ce que chaque élément du dossier soit conforme avant d'atteindre le stade de l'approbation des pièces. Grâce aux formations continues et à l'approche proactive du contrôle qualité, le PPAP contribue de manière significative à la satisfaction du client et à la pérennité de l'entreprise sur le marché.
Les étapes clés du PPAP
Les étapes essentielles de la soumission PPAP
Le processus de soumission PPAP est composé de plusieurs étapes cruciales afin de garantir la qualité et la conformité des pièces de production. Voici les étapes principales qui composent ce processus :- Plan de contrôle et inspection : Le fournisseur développe un plan de contrôle basé sur les éléments de conception pour surveiller le processus de fabrication et veiller à ce que chaque produit réponde aux exigences définies par le client.
- Analyse des modes de défaillance et leurs effets (AMDE) : Une analyse approfondie est réalisée pour identifier les modes potentiels de défaillance dans le processus de production et leurs impacts, afin de prendre des mesures correctives préventives.
- Données justificatives et échantillons produits : Durant la phase de soumission, le fournisseur doit fournir des échantillons de pièces ainsi que des données montrant que la production répond aux attentes de qualité spécifiées.
- Niveau PSW et approbation : Après soumission des pièces de production, le dossier PPAP est évalué et un niveau de PSW (Production Submission Warrant) est attribué pour certifier que les pièces répondent aux normes du processus d'approbation fixées par les clients.
L'impact du PPAP sur la chaîne d'approvisionnement
L'impact positif du processus PPAP sur la chaîne d'approvisionnement
Le processus PPAP joue un rôle essentiel dans la gestion de la qualité au sein de la chaîne d'approvisionnement. Pour commencer, il garantit que les pièces fournies répondent aux exigences des clients avant leur entrée en production. Ce contrôle rigoureux aide à réduire les défauts, augmentant ainsi la qualité des produits finis. Les fournisseurs, grâce au processus d'approbation PPAP, transmettent un dossier complet comportant toutes les données justificatives nécessaires, assurant que chaque aspect du produit a été vérifié et validé. Voici quelques éléments clés de l'impact du PPAP :- Amélioration de la communication : Les rapports PPAP renforcent la communication entre clients et fournisseurs, clarifiant les attentes et les standards requis.
- Réduction des risques : En établissant un plan de contrôle détaillé, le PPAP permet de mieux cerner les risques potentiels et d'anticiper les modes de défaillance grâce à l'analyse des modes de défaillance et de leurs effets (AMDE).
- Contrôle de la production : L'approbation des pièces de production assure que les éléments de la soumission PPAP ont été testés et validés à différents niveaux, diminuant les retours et les désaccords.
- Optimisation du processus : En intégrant le PPAP dans le cadre plus large de l'APQP (planification avancée de la qualité du produit), les entreprises peuvent mieux gérer le changement dans la qualité industrielle et garantir une livraison sans accroc des produits aux clients.
Défis courants dans la mise en œuvre du PPAP
Défis rencontrés lors de l'application du processus PPAP
Dans l'industrie, la mise en œuvre du processus PPAP présente plusieurs défis qui peuvent affecter la qualité et la satisfaction des clients. Ces défis nécessitent une attention particulière pour garantir l'efficacité du processus et la conformité aux exigences des clients.- Complexité du processus : Le PPAP repose sur une série d'étapes complexes qui exigent une compréhension approfondie des éléments requis, tels que le dossier PPAP, les données justificatives et les échantillons de produit.
- Exigences du client : Chaque client peut avoir des exigences spécifiques pour le PPAP, ce qui nécessite une adaptation du processus de soumission et une communication constante entre le fournisseur et le client.
- Formation et compétences : La formation adéquate du personnel est essentielle pour s'assurer que toutes les parties prenantes comprennent bien le processus d'approbation des pièces et la production. Une analyse des modes de défaillance et des effets est souvent nécessaire.
- Intégration des données : Collecter et analyser les données nécessaires pour le plan de contrôle et la niveau PSW peut être un processus long et sujet à des erreurs si mal géré.
- Maintien de la qualité : Assurer la qualité constante des pièces produites pendant le processus fabrication est un défi continu, où des contrôles rigoureux doivent être intégrés dans la production et les processus de conception.
Les avantages du PPAP pour les entreprises
Avantages pour les entreprises de l'intégration du PPAP
L'intégration du processus PPAP apporte de nombreux avantages aux entreprises, influençant plusieurs aspects de leur fonctionnement. Le PPAP, ou Production Part Approval Process, est conçu pour assurer que toutes les spécifications et exigences du client sont respectées avant la production en grande série. Voici quelques-uns des principaux bénéfices que les entreprises peuvent tirer du PPAP :- Amélioration de la qualité des produits : En suivant le PPAP, les entreprises peuvent garantir que les pièces et les éléments respectent les normes de qualité requises. Le processus formel de soumission et d'approbation aide à identifier et corriger les défauts potentiels avant qu'ils ne soient intégrés dans la ligne de production.
- Réduction des coûts : Grâce à une meilleure détection et gestion des modes de défaillance potentiels, ainsi qu'à l'optimisation des processus de fabrication, le PPAP permet de réduire les rebuts et les retours de produits.
- Confiance accrue des clients : Les entreprises qui utilisent le PPAP démontrent un engagement envers la qualité, ce qui peut renforcer la confiance des clients dans leurs produits. Cela s'avère crucial pour la fidélisation des clients et le développement de relations à long terme.
- Collaboration améliorée avec les fournisseurs : Le processus PPAP implique une étroite collaboration entre l'entreprise et ses fournisseurs pour s'assurer que les exigences des clients sont bien comprises et respectées à tous les niveaux de la chaîne de production.
- Réglementation et conformité : La mise en œuvre du PPAP aide souvent les entreprises à se conformer aux normes et réglementations en vigueur dans leur secteur, en structurant leur approche de la gestion de la qualité.
- Favorise l'amélioration continue : Le recours au PPAP incite les entreprises à adopter des pratiques d'amélioration continue, telles que l'APQP (Advanced Product Quality Planning) et l'analyse des modes de défaillance et de leurs effets. Ces méthodes encouragent l'identification proactive des opportunités d'amélioration.
Tendances futures du PPAP dans l'industrie
Évolution future et intégration du processus PPAP
À mesure que l'industrie évolue, le processus PPAP s'adapte pour répondre aux nouvelles exigences en matière de qualité et de production. Avec l'avancée des technologies et des méthodologies, plusieurs tendances futures sont à prévoir :- Automatisation accrue : Avec l'avènement des technologies numériques, l'automatisation du processus PPAP, notamment dans le contrôle des pièces et des produits, va s'intensifier. Les données justificatives de la conformité des pièces bénéficieront de systèmes intégrés permettant une meilleure traçabilité et transparence.
- Intégration approfondie avec l'APQP : Le lien entre PPAP et APQP se renforcera, optimisant ainsi le plan de contrôle et la qualité des produits finis. Cette intégration assure une synchronisation continue entre la conception et la production.
- Emphase sur la formation continue : Les fournisseurs et les clients devront investir dans la formation sur le processus d'approbation des pièces (PSW) pour garantir une compréhension claire des exigences et une mise en œuvre efficace.
- Utilisation de l'analyse des modes de défaillance : L'intégration d'analyses poussées, comme l'analyse des modes de défaillance et leurs effets, permettra de prévoir et de prévenir les problèmes potentiels avant qu'ils n'affectent la production.